Description
Following is the shape of Inconel 718,Inconel ALloy 718, Alloy 718,UNS N07718 forging steel material that we could do is:Inconel 718 Forged Steel round bars square bars Flat bars Rectangles Bars Rods,Inconel ALloy 718 Forged forging steel rings seamless rolled rings,Alloy 718 Forged Forging Steel Hubs housing shell Sleeves Bushes Bushing Cases Hollow Bars,UNS N07718 Forged Forging Steel Discs Disks Blocks plates,Inconel 718 Forged Forging Steel Pipe Tubes Tubings Piping Shells Casings Case barrels Housings.
Following is forging products of Inconel 718,Inconel ALloy 718, Alloy 718,UNS N07718 material that is used in following industry
Alloy 718 forged forging gas separator protector intake HPS splined shaft
Inconel ALloy 718 forging Forged Drilling Pipes Tubes Drill Rods drill Drilling collar
Alloy 718 Forged Forging Turbine and Compressor Labyrinth Shaft Seals
Inconel 718 Forging Copper brass Extrusion Dies, dies case,extrusion stems,
UNS N07718 Forging forged Copper Aluminum Magnesium Extrusion Presses Container Liners Inner Intermediate Liners
Inconel ALloy 718 Forged/Forging Blow Out Blowout Preventer RAM Annular dual Bop Body Bodies Block
Alloy 718 Forged Forging drilling tools,risers,connectors,flexible joint ,seals,flanges gasket
Inconel 718 Forged Forging Valve Balls,valve Bonnets,valve Body Bodies ,valve Stems,valve closures, valve seat rings, valve core, valve discs,for H type two way 2‐way one way back pressure valves, ball valve,check valve,gate valve
ALloy 718 Forged Forging Steel nuclear Power reactor coolant pumps Rotor Impellers
Inconel 718 forged steel Mechanical Seal Discs
Inconel Alloy 718 Forged Forging Steel Butterfly Valve Main Shafts Spindles
Alloy 718 Forged Forging Swept branches outlets steel fittings swept saddles
Inconel 718 Forged Forging downhole drilling tool Mud Motor Splined Drive shafts,Down hole Electric electrical submersible pumps ESP motor Splined Shaft
Inconel 718 Forged Forging Gas Air Compressor Rotor
Forged Forging Gas Steam Turbine Engine Tie Rods
Inconel Alloy 718 Forged Forging Steels Christmas Trees wellhead Spool Body Bodies cylinder
Alloy 718 Forged Forging venturi cone meter Body Bodies Blocks
UNS N07718 Forged Forging Steel gate valves Body Bodies bespoke flat bars
Inconel 718 forged steel Flowseal cryogenic High Performance BV Butterfly Valves HPBV shaft
Inconel 718 forging steel Oil measurement valve Spool Ultrasonic flow meter bodies Body
Inconel Alloy 718 Forged Forging Steel double studded adapter flange
Inconel Alloy 718 Forged Forging Steel integral Mud Flange Flanged outlet Studded crosses
UNS N07718 Forged Forging Steel Casing Heads,Tubing Heads,Casing Hangers,Tubing Hangers,Tubing Spools,Casing Spools,Spacer Spools
Inconel Alloy 718 Forged Forgig Steel nuclear reactor coolant pump Casing Shells body bodis blocks,nuclear reactor coolant pumps containment seal chamber Rooms,nuclear reactor coolant pumps containment seal chamber Rooms
Inconel Alloy 718 Forged Forging turbomachinery turbo centrifugal compressor Impeller,Compressor Shrouded Impellers
Inconel Alloy 718 Forged Forging Steel Forged Single Double Bossed boss Blanks FLANGED BOSSES
Inconel Alloy 718 Forged Forging Steel PUMP Casing cover.PUMP BARREL,pump impeller,pump shafts, pump housing, pump shells,pump body,pump wear rings,pump case casing.
Alloy 718 Forged Forging forge Steel transition Cone
UNS N07718 Forged Forging Steel Pressure Vessel Reactor Nozzles
Alloy 718 Forged Forging Gas Compressor Turbine Blades steel Flat Rectangles Bars
Alloy 718 Forged Forging Gas steam turbine disks, turbine impeller,turbine blisk,turbine discs,turbine wheel discs
Inconel Alloy 718 Forging Steel Forging Forged Gas Steam Turbine Doubled-headed Double end Studs Fasteners Bolts bolting
Inconel Alloy 718 Forging Steel gas steam Turbine Guide Rings,seal rings Labyrinth Rings Packing Seal Diaphragm & Seal Ring Rotor End Rings contours Casing Rings
Inconel Alloy 718 Forged Forging Steel Gas Steam turbine diaphragm diapharagm nozzles
Inconel 718 Forged Forging Gas Turbine LPT 1st & 2st 2nd Stg Stage Turbine Case Casings
Inconel 718 Forged Forging Steel power plant steam turbine control reheat valve disc Disk
UNS N07718 Forged forging Gas Steam Turbine Valve Spindles/Stems/Rods,
Inconel 718 Forging Steel Gas Steam Turbine MSV/GV/CV/CRV Valve Seats, Valve Cores, Valve Sleeves Spools,,Main Steam Valve Covers Bonnets Sleeves
Inconel 718 forged forging steel pipes tubes shells piping tubing barrels housing, tube sheets,baffle plates, nozzles, channel flanges for boiler, heat exchanger,pressure vessel,reactors, heaters
UNS N07718 Forged Forging Nickel Alloy Bore Protector
FOllowing is chemical compostion of Inconel ALloy 718 forged steel rings
Element |
C |
Si |
Mn |
P |
S |
Cr |
Ni |
Mo |
Nb |
Ti |
Al |
%min |
|
|
|
|
|
17.0 |
50.0 |
2.80 |
4.75 |
0.65 |
0.20 |
%max |
0.08 |
0.35 |
0.35 |
0.015 |
0.015 |
21.0 |
55.0 |
3.30 |
5.50 |
1.15 |
0.80 |
Element |
Co |
Ta |
B |
Cu |
Pb |
Bi |
Se |
Fe |
|
||
%min |
|
|
|
|
|
|
|
|
|||
max |
1.00 |
0.05 |
0.006 |
0.30 |
0.0005 |
0.00003 |
0.0003 |
Rem. |
Following of Inconel 718 forging parts heat treatment nechanical property Delivery condition :
Shape |
Condition |
Temp T°C |
Proof strength Rpo₂MPa min |
Tensile strength Rm MPa l/tr min 1) |
Elongation after fracture A₄%(Lo=4D₀) /tr min 1) |
Reduction of are Z% l/tr min 1) |
Hardness HB 2) |
bar |
3) |
20 |
1034 |
1276/1241 |
12/6 |
15/8 |
min 331 (400-450) |
bar |
3) |
650 |
862 |
1000/965 |
12/6 |
15/8 |
|
forging |
3) |
20 |
1034 |
1276/1241 |
12/10 |
15/12 |
min 331 (400-450) |
forging |
3) |
650 |
862 |
1000/965 |
12/10 |
15/12 |
|
1)l=longitudinal,tr =transverse.
Direction of the longitudinal axis of the test piece in relation to the principal deformation direction of the blank.
2)Values given in brackets are not binding.
3)Solution annealed and aged
Stress repcture of inconel 718 steam turbine forged parts as following
Test sample |
Shape |
Condition |
Temp T℃ |
Stress MPa min |
Time to rupture h min |
Elongation after fracture A₄%(Lo=4D₀) min |
1) |
AIl |
2) |
649±2 |
689 |
23 |
4 |
1)Both notched and smooth specimens shall be tested.Notched specimenshall not rupture before smooth.
2)Solution annealed and aged
3)The test may be conducted using a higher load.
4)The test may be conducted using incremental loading after 23 h.
Heat treatment way of inconel 718 forged round bars is as following
941-1010±14°C Holding time commensurates with thickness.Air cooling or faster. 2-4-2 Ageing
720±8°C/8 h,Cooling in the furnace to 620±8°C,This temperature shall be held to a total ageing time of 18 h,followed by air cooling.
All documentation of finished inconel 718 forging material inspection document must be written in English.
All results must be given in accordance with the Sl system.
All documentation shall be well readable without risk of incorrect interpretation.
Inspection certificate EN 10204-3.1,with heat analysis and results of all testing in accordance with 6 Delivery inspection.
Heat treatment certificate,with information on the temperature and soaking time. 2-3 Surplus test material shall be separated from the blank and stored by the supplier for a minimum of three month after accepted delivery.If the test material is to be delivered,this will be stated in the purchase order or in a separate message.
A“Declaration of conformity”in accordance with EN ISO/IEC 17050 may be accepted as reporting,if this is stated in an agreement with the purchaser.
The declaration shall contain:All information necessary for full tracking to delivered goods and/or process used.
- Reference to all inspection and test reports.
ALl our inconel 718 forging material shall file all subordinated documents at least 15 years after the delivery of the goods or the service.
Following is inspection standard of Alloy 718 forged parts
ASTM A604 Standard test methods for macroetch testing of consumable electroderemelted steel bars and billets
ASTM E112 Standard test methods for determining average grain size
EN ISO 6892-1:20 Metallic materials -Tensile testing -Part 1:Method of test at ambient temperature
ISO 204:2009 Metallic materials -Uniaxial creep testing in tension -Method of test
EN 10204 Metallic products -Types of inspection documents
EN ISO/IEC 17050:2004 Conformity assessment -Supplier's declaration of conformity -General requirements
All our inconel 718 forged material must give the material a required purity necessary for the application in following melting methods
one is triple melted material,VIM+ESR+VAR., the another one is double melted material,VIM+VAR.
All our UNS N07718 forging material shall be thoroughly worked,homogenous and free from blisters, cracks and injurious slag inclusions.
Grain size requirement of inconel 718 forging bars
The following requirements shall apply to grain size determination unless otherwise specified in the material specification:
ASTM average grain size no.5 or finer.Occasional grains max no.4.
Macroetching shall be performed after rough machining.Imperfections shall not be worse than stated in following table:
Class |
Condition |
Severity |
1 |
Freckles |
A |
2 |
White spots |
A |
3 |
Radial segregation |
Not allowed |
4 |
Ring pattern |
C |
Inspection and testing shall be carried out after final heat treatment (ageing)of the inconel 718 forged blank.
Heat treatment shall be carried out after working,before removal of the test specimens,with well cleaned surfaces of the blank.The specimens shall be removed before ultrasonic testing of the blank.
Mechanical testing shall be carried out on integrally forged or rolled specimens.The position and number of the specimens shall be shown on the blank drawing or shall be agreed in each case.
Tensile testing at 20°C and 650°C.At least one test piece from one specimen per part and temperature.
Creep rupture testing of one test piece from one specimen from each part at 650℃.
Hardness testing of each specimen.
UItrasonic testing shall be carried out with a method and an extent to be agreed upon. A special testing procedure specification shall be established for each component
Macroetching shall be carried out on each part.Inspection shall check for grain size,segregations and surface defects.
Microstructure.If no defects are revealed in macroetching,a micro examination shall be carried out on areas marked on drawing.
If defects are revealed on any area,a specific micro examination of the area shall be performed and reported.
Tensile testing:EN ISO 6892-1.
Creep rupture testing:ISO 204.
UItrasonic testing shall be carried out in accordance with agreed testing procedure specification.
Macroetching:ASTM A604.
Grain size estimation:ASTM E112
Each part shall be stamped with:
The purchaser's part number
The purchaser's purchase number
Following is one testing requirement of inconel 718 forged bars as per API 6A 120KSI
CHEMICAL COMPOSITION LIMITS of inconel 718 forged bars as per API 6A 120KSI
An analysis of each heat of steel shall be made to determine the weight percentages of the elements specified below. Chemical composition shall be determined on a remelt ingot basis.
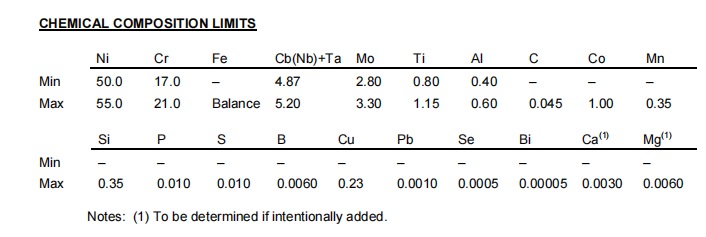
TENSILE PROPERTY REQUIREMENTS of inconel 718 forged bars as per API 6A 120KSI
Tensile test specimens shall be removed from a Qualified Test Coupon (QTC) as described in API Spec 6A and tests performed
at room temperature in conformance with the procedures set out in ASTM A370.
A minimum of one Tensile test may qualify a heat of material, and the components produced from that heat,
if the test results satisfy the requirements specified below.
Minimum Tensile Strength, psi 150,000 (1034 MPa)
Minimum Yield Strength, psi, 0.2% Offset 120,000 (827 MPa)
Minimum Elongation in 2" Gauge Length 20%
Minimum Reduction of area, ≤ 10 in (25.4 cm) cross section 35%
Minimum Reduction of area, > 10 in (25.4 cm) cross section 25%
If the results of the Tensile test(s) do not satisfy the specified requirements, then a retest of two additional test specimens
(removed from the same QTC with no additional heat treatment) may be performed.
The results of these tests shall satisfy the specified requirements.
HARDNESS TEST REQUIREMENTS of inconel 718 forging bars as per API 6A 120KSI
Hardness testing shall be performed in accordance with the procedures in ASTM E10 or ASTM E18.
At least one Rockwell or Brinell hardness test shall be performed on each forging or bar after the final heat treatment cycle.
A minimum of one hardness test shall be performed on the QTC after the final heat treatment cycle.
Test results shall satisfy the requirements specified below.
Hardness Range, HBW 298 – 363 (32 – 40 HRC)
CHARPY V-NOTCH IMPACT REQUIREMENTS (10mm x 10mm)
Impact Testing shall be performed in conformance with the procedures set out in ASTM A 370 using the Charpy V Notch technique. A set of three transverse or longitudinal impact specimens shall be removed at mid-radius and tested at or below -75°F (-60°C). Specimens oriented transverse to the primary direction of grain flow shall be used unless the size or geometry of the QTC does not permit transverse orientation (i.e. material less than 3” [76mm] in cross section). For material less than 3” (76mm) in cross section, specimens may be oriented in the longitudinal direction. These three impact specimens may qualify a heat of material if the test results satisfy the Minimum Average Value, and no more than one of the three tests falls below the required Minimum Average, and its value is not less than the Single Minimum Value.
Transverse
Longitudinal
QTC Cross
Minimum
Single
Lateral
Minimum
Single
Lateral
Section Thickness
Average
Value
Minimum
Value
Expansion
Average
Value
Minimum
Value
Expansion
in (cm)
ft-lbf (J)
ft-lbf (J)
in (mm)
ft-lbf (J)
ft-lbf (J)
in (mm)
< 3 (7.6)
–
–
–
50 (68)
45 (61)
0.015 (0.38)
3 (7.6) ≤ 10 (25.4)
35 (47)
30 (41)
0.015 (0.38)
–
–
–
> 10 (25.4)
30 (41)
27 (37)
0.015 (0.38)
–
–
–
If the results of the Impact test(s) do not satisfy the specified requirements, then a retest of three additional specimens (removed from the same location within the same QTC with no additional heat treatment) may be made, each of which shall exhibit an impact value equal to or exceeding the Minimum Average Value.
MATERIAL QUALIFICATION of inconel 718 forged bars as per API 6A 120KSI
The properties exhibited by the Qualification Test Coupons (QTC) shall represent the properties of the material comprising the production parts it qualifies. A single QTC may be used to represent the Impact and/or Tensile properties of the parts produced form the same heat, provided it satisfies the requirements of API Spec 6A.
ALLOWABLE MELTING PRACTICE(S) of inconel 718 forged bars as per API 6A 120KSI
Material supplied to meet this specification shall be melted by one of the following sequence of processes:
Step 1: Basic electric furnace (EF)
a) Step 2: Argon oxygen decarburization (AOD) or vacuum oxygen decarburization (VOD)
b) Step 3: Vacuum arc remelting (VAR)
c) Step 4: Additional VAR
Step 1: Vacuum induction melting (VIM)
a) Step 2: Vacuum arc remelting (VAR)
8.4. Step 1: Vacuum induction melting (VIM)
a) Step 2: Eletroslag remelting (ESR)
FORMING PRACTICE(S) of inconel 718 forged bars as per API 6A 120KSI
All materials shall be formed using a hot working practice(s) which produces a wrought structure throughout. The minimum total hot work reduction ratio shall be 3.75:1. When not proprietary, vendor shall document hot working practices.
REQUIRED HEAT TREATMENT of inconel 718 forged bars as per API 6A 120KSI
All heat treating of parts and QTCs shall be performed with production type equipment
meeting the requirements specified by the manufacturer.
The material temperature shall be measured by use of either a furnace thermocouple, a
contact surface thermocouple or a heat sink as specified in API Spec 6A. The hold time shall not commence until the contact surface thermocouple or a heat sink reaches at least the minimum required temperature.
Material supplied to meet this specification shall be solution annealed and age hardened in accordance with the following procedure:
Heat Treat Process | Holding Temperature | Holding Time | Media | |||||||||||||
Solution Anneal |
1870°F – 1925°F (1021°C – 1052°C) |
1 to 2-1/2 hrs | Air cool or faster(1) | |||||||||||||
Age Harden |
1425°F – 1475°F (774°C – 802°C) |
6 to 8 hrs | Air cool or faster(1) |
Notes: (1) For Water or Polymer Quenching, the temperature of the water or water based quenching medium shall not exceed 100°F (38°C) at the start of the quench, nor exceed 120°F (49°C) at the completion of the quench. Starting and ending quench media temperatures shall be documented.
Following is heat treatment chart of inconel 718 forged bars as per API 6A 120KSI
MICROSTRUCTURAL REQUIREMENTS of inconel 718 forged bars as per API 6A 120KSI Sample(s) of material from each remelt ingot per heat treat lot shall be subjected to a microstructural analysis.
Longitudinal microstructural samples shall be etched for examination with an etchant suitable to reveal detrimental phases. The samples shall be examined at 100X and 500X using light microscopy.
The microstructure shall be free of continuous grain boundary secondary phases. The microstructure shall be free of acicular delta phase in and growing from grain boundaries. No topological duplex grain size as defined and measured per ASTM E 1181 is allowed.
The average grain size shall be predominantly No.3 or finer for ≤10 in (25.4 cm) cross section and No.2 or finer for >10 in (25.4 cm) cross section. The average grain size shall be determined in accordance with ASTM E 112 and reported.
NON-DESTRUCTIVE EXAMINATION (NDE) REQUIREMENTS of inconel 718 forged bars as per API 6A 120KSI
Material supplied to this specification shall be capable of passing Ultrasonic Testing per API Spec 6A, PSL-3.
DEVIATIONS AND WAIVERS of inconel 718 forged bars as per API 6A 120KSI
If the material supplier wishes to apply for a waiver to any of the requirements in this document then they shall submit a written request prior to the delivery of the material. Signed documents approving any accepted deviations shall be submitted with the delivery of material and MTRs.
MATERIAL TEST REPORTS (MTRs) of inconel 718 forged bars as per API 6A 120KSI
The material supplier shall provide a certified test report containing the following information as a minimum:
Tensile Test results
Hardness Test results
Chemical Analysis results
Impact Test temperature, orientation and results
Melt Practice used, including melt source
Total hot work reduction ratio (may be reported as a minimum value)
Actual heat treatment times and temperatures
Quench media used, including quench media starting and ending temperatures
Statement(s) that the material complies with the microstructural analysis requirements
The absence of any response or documentation required shall represent a rejectable non- conformance to this specification.
SPECIAL REQUIREMENTS of inconel 718 forged bars as per API 6A 120KSI : API SPEC 6A PSL-4 Material supplied to API Spec 6A PSL-4 shall have the following additional requirements:
Heat Treatment Temperature for inconel 718 forged bars as per API 6A 120KSI PSL-4 material shall be determined by using a heat sink, as specified in API Spec 6A. The heat sink used shall be documented and the temperature reported by the manufacturer.
inconel 718 forged bars as per API 6A 120KSI Material supplied to this specification for PSL-4 shall be capable of passing Ultrasonic Testing per API Spec 6A, PSL-4.