Description
Jiangsu Liangyi professional manufacturer of Ph13-8Mo,PH 13-8 Mo,XM-13,UNS S13800,XM13,13-8 PH,Ph 13/8 Mo,GRADE 13-8,PH 13/8MO open die forging parts and seamless rolled steel forged rings in in delivery Precipitation hardening condition of Ph13-8Mo H950,,Ph13-8Mo H1000,Ph13-8Mo H1025,Ph13-8Mo H1050,Ph13-8Mo H1100,Ph13-8Mo H1150 from china
Following is the shape of Ph13-8Mo,PH 13-8 Mo,XM-13,UNS S13800,XM13,13-8 PH,Ph 13/8 Mo,GRADE 13-8,PH 13/8MO forging steel material that we could do is:Ph13-8Mo Forged Steel round bars square bars Flat bars Rectangles Bars Rods,UNS S13800 Forged forging steel rings seamless rolled rings,Ph 13/8 Mo Forged Forging Steel Hubs housing shell Sleeves Bushes Bushing Cases Hollow Bars,XM13 Forged Forging Steel Discs Disks Blocks plates,XM-13 Forged Forging Steel Pipe Tubes Tubings Piping Shells Casings Case barrels Housings.
Following is forging products of Ph13-8Mo,PH 13-8 Mo,XM-13,UNS S13800,XM13,13-8 PH,Ph 13/8 Mo,GRADE 13-8,PH 13/8MO material that is used in following industry
Ph13-8Mo Forged Forging Gas Compressor Turbine Blades steel Flat Rectangles Bars
UNS S13800 Forged Forging Gas steam turbine disks, turbine impeller,turbine blisk,turbine discs
XM-13 Forging Steel Forging Forged Gas Steam Turbine Doubled-headed Double end Studs Fasteners Bolts
PH 13-8 Mo Forging Steel gas steam Turbine Guide Rings,seal rings Labyrinth Rings Packing Seal Diaphragm & Seal Ring Rotor End Rings contours Casing Rings
Ph 13/8 Mo forged forging steel pipes tubes shells piping tubing barrels housing, tube sheets, nozzles, channel flanges for boiler, heat exchanger,pressure vessel,reactors, heaters
Ph13-8Mo Forged Forging ultra high pressure water jet Waterjet cutting Machine Cutter Hydraulic Cylinder,accumulator attenuator
UNS S13800 forged steel ultra high pressure water jet Waterjet cutting Machine Cutter intensifier pump Sealing Heads
XM-13 Forged Forging Valve Balls,valve Bonnets,valve Body Bodies ,valve Stems,valve closures, valve seat rings, valve core, valve discs,for H type two way 2‐way one way back pressure valves, ball valve,check valve,gate pump
XM13 Forged Forging Steel nuclear Power reactor coolant pumps Rotor Impellers
XM-13 Forged Forging Marine Ship Boat Propeller Shafts
Ph13-8Mo forging steel injection molding dies, tooling,dies blocks
UNS S13800 Forged Forging downhole drilling tool Mud Motor Splined Drive shafts,Down hole Electric electrical submersible pumps ESP motor Splined Shaft
Ph 13-8 Mo Forged Forgig Steel nuclear reactor coolant pump Casing Shells body bodis blocks,nuclear reactor coolant pumps containment seal chamber Rooms,nuclear reactor coolant pumps containment seal chamber Rooms
XM-13 Forged Forging turbomachinery turbo centrifugal compressor Impeller,Compress
Ph13-8Mo Forged Forging Steel PUMP Casing cover.PUMP BARREL,pump impeller,pump shafts, pump housing, pump shells,pump body,pump wear rings
Ph 13/8 Mo Forged Forging forge Steel transition Cone
Ph13-8Mo forging material shall be multiple melted using vacuum induction primary melting followed by either vacuum consumable electrode remelting for Type 1 or, when specified, electroslag remelting for Type 2.
Ph13-8Mo is a stainless steel with approximately 13% chromium and 8% nickel content that has good resistance to corrosion in general as well as to stress corrosion cracking. PH 13-8 Mo offers better mechanical properties in demanding environmental conditions in comparison to other materials based on iron. Precise control of the microstructure is achieved through vacuum melting and remelting. Medium to high strength can be achieved through precipitation hardening aging treatments.
Ph13-8Mo is is widely us in Aerospace components,Injection molding equipment,Waterjet cutting equipmentPetrochemical industries,Nuclear industries
FOllowing is forging standard of UNS S13800 forged steel rings, :
AMS 5629
AMS 5864
AMS STD 2154
ASTM A564
ASME SA564
ASTM A705 (capability)
ASTM F899
Bell 299-947-361
Boeing HMS 6-1105
Rockwell ST0160LB0013
Schlumberger SH350516, 100127819, and T1037098
FOllowing is chemical compostion of Ph13-8Mo,PH 13-8 Mo,XM-13,UNS S13800,XM13,13-8 PH,Ph 13/8 Mo,GRADE 13-8,PH 13/8MO forged steel rings in accordance with ASTM A751,
Element | Min | Max | ||||
Carbon | -- | 0.05 | ||||
Manganese | -- | 0.10 | ||||
Silicon | -- | 0.10 | ||||
Phosphorus | -- | 0.010 | ||||
Sulfur | -- | 0.008 | ||||
Chromium | 12.25 | 13.25 | ||||
Nickel | 7.50 | 8.50 | ||||
Molybdenum | 2.00 | 2.50 | ||||
Aluminum | 0.90 | 1.35 | ||||
Nitrogen | -- | 0.010 |
Macrostructure test of Ph13-8Mo forging material is as following
Visual examination of transverse full cross-sections from bars, billets, , and stock for forging, etched in hot hydrochloric acid in accordance with ASTM A604, shall show no pipe or cracks. Porosity, segregation, inclusions, and other imperfections for product 81 square inches (523 cm2) and under in nominal cross-sectional area shall be no worse than the macrographs of ASTM A604 shown in Table 2. For product greater than 81 square inches (523 cm2) in cross sectional area, the macrostructure shall meet the requirements for product under 81 square inches (523 cm2) and under in nominal cross-sectional area or the criteria shall be approved by the cognizant engineering authority.
Table 2 - Macrostructure limits
Class 1 ,Condition Freckles, Severity A
Class 2 ,Condition White Spots, Severity A
Class 3 ,Condition Radial Segregation, Severity A
Class 4 ,Condition Ring Pattern, Severity B
Shall be ASTM No. 5 or finer for product up to 3.00 inches (76.2 mm) in nominal diameter, least distance between parallel sides and shall be ASTM No. 4 or finer for product 3.00 inches (76.2 mm) and over in nominal diameter, or least distance between parallel sides, determined in accordance with ASTM E112.
Precipitation hardening conditions of Ph13-8Mo forged round bars is as follow
H950 950 °F ± 10 °F (510 °C ± 6 °C) 4 hours + 30 / -0 minutes
H1000 1000 °F ± 10 °F (538 °C ± 6 °C) 4 hours + 30 / -0 minutes
H1025 1025 °F ± 10 °F (552 °C ± 6 °C) 4 hours + 30 / -0 minutes
H1050 1050 °F ± 10 °F (566 °C ± 6 °C) 4 hours + 30 / -0 minutes
H1100 1100 °F ± 10 °F (593 °C ± 6 °C) 4 hours + 30 / -0 minutes
H1150 1150 °F ± 10 °F (621 °C ± 6 °C) 4 hours + 30 / -0 minutes
Following of Ph13-8Mo forging parts heat treatment Delivery condition :
Table 4A - Minimum tensile properties after precipitation heat treatment, inch/pound units | ||||||||||||||||||||
Condition |
Specimen Orientation |
Tensile Strength ksi |
Yield Strength at 0.2% Offset ksi |
Elongation in 4D % |
Reduction of Area % |
|||||||||||||||
H950 |
Longitudinal Transverse |
220 220 |
205 205 |
10 10 |
45 35 |
|||||||||||||||
H1000 |
Longitudinal Transverse |
205 205 |
190 190 |
10 10 |
50 40 |
|||||||||||||||
H1025 |
Longitudinal Transverse |
185 185 |
175 175 |
11 11 |
50 45 |
|||||||||||||||
H1050 |
Longitudinal Transverse |
175 175 |
165 165 |
12 12 |
50 45 |
|||||||||||||||
H1100 |
Longitudinal Transverse |
150 150 |
135 135 |
14 14 |
50 50 |
|||||||||||||||
H1150 |
Longitudinal Transverse |
135 135 |
90 90 |
14 14 |
50 50 |
|||||||||||||||
properties precipitation treatment, | ||||||||||||||||||||
Condition |
Specimen Orientation |
Tensile Strength MPa |
Yield Strength at 0.2% Offset MPa |
Elongation in 4D % |
Reduction of Area % |
|||||||||||||||
H950 |
Longitudinal Transverse |
1517 1517 |
1413 1413 |
10 10 |
45 35 |
|||||||||||||||
H1000 |
Longitudinal Transverse |
1413 1413 |
1310 1310 |
10 10 |
50 40 |
|||||||||||||||
H1025 |
Longitudinal Transverse |
1276 1276 |
1207 1207 |
11 11 |
50 45 |
|||||||||||||||
H1050 |
Longitudinal Transverse |
1207 1207 |
1138 1138 |
12 12 |
50 45 |
|||||||||||||||
H1100 |
Longitudinal Transverse |
1034 1034 |
931 931 |
14 14 |
50 50 |
|||||||||||||||
H1150 |
Longitudinal Transverse |
931 931 |
621 621 |
14 14 |
50 50 |
Following is testing way of Ph13-8Mo forging mechanical property
Unless otherwise specified, the strain rate shall be set at 0.005 in/in/min (0.005 mm/mm/min) and maintained within a tolerance of ±0.002 in/in/min (0.002 mm/mm/min) through 0.2% offset yield strain. After the yield strain, the speed of the testing machine shall be set between 0.05 and 0.5 in/in (0.05 and 0.5 mm/mm) of the length of the reduced section (or distance between the grips for specimens not having a reduced section) per minute. Alternatively, an extensometer and strain rate indicator may be used to set the strain rate between 0.05 and 0.5 in/in/min (0.05 and 0.5 mm/mm/min).
Longitudinal tensile property requirements apply to specimens taken in the longitudinal direction from forged barsto specimens taken from forgings with axis of specimen in the area of gage length varying not more than 15 degrees from parallel to the forging flow lines, and to specimens taken in the circumferential direction from flash welded rings.
Transverse tensile property requirements of Ph13-8Mo forging parts apply to specimens taken approximately perpendicular to the longitudinal direction of bars and extrusions, to specimens taken from forgings with axis of specimen in the area of gage length varying not more than 15 degrees from perpendicular to the forging flow lines, and to specimens taken in either the radial or axial direction from flash welded rings.
Transverse tensile property requirements of Ph13-8Mo forging parts apply only to products from which a test specimen not less than 2-1/2 inches (63.5 mm) long or 1/2 inch (12.7 mm) x 1/2 inch (12.7 mm) cross-section can be take. If the cross-sectional dimensions of the product permit, the transverse testing shall be of the short-transverse (ST) direction; otherwise, the orientation shall be in the long transverse (LT) direction.
Following is inspection standard of Ph13-8Mo,PH 13-8 Mo,XM-13,UNS S13800,XM13,13-8 PH,Ph 13/8 Mo,GRADE 13-8,PH 13/8MO forging material
ASTM A370 Mechanical Testing of Steel Products
ASTM A604 Macroetch Testing of Consumable Electrode Remelted Steel Bars and Billets
ASTM A751 Test Methods, Practices, and Terminology for Chemical Analysis of Steel Products
ASTM E112 Determining Average Grain Size
ASTM E140 Hardness Conversion Tables for Metals Relationship Among Brinell Hardness, Vickers Hardness, Rockwell Hardness, Superficial Hardness, Knoop Hardness, Scleroscope Hardness, and Leeb Hardness
Following is one inspection certificate of ph-8 forged round bars in anneal treatment
Quality Inspection Certificate acc. to EN10204-3.1 |
|||||||
Product Description |
Round bars |
Material Grade |
PH13-8 |
||||
CLients |
|
Purchase Order # |
PO2425/00058 |
||||
Melting Method |
VIM+ESR+VAR |
Quantity |
1 |
||||
Heat # |
DV240533-E0540B-V0601 |
|
|
||||
Heat Treat Lot # |
2023091904 |
Size (in) |
440MM diameter, 830MM length |
||||
Delivery Condition |
Forged,solution annealed treatment, machined |
Ferrite content:0.2% |
|||||
Grain size |
ASTM 6.5 |
|
|||||
Material Specification |
AMS 5629 |
|
|
||||
1.35
Chemical Composition
per ASTM A751 |
|
C% |
Mn% |
Si% |
P% |
AL% |
S% |
Cr% |
Mo% |
N% |
Ni% |
Min |
|
|
|
|
0.9 |
|
12.25 |
2.0 |
|
7.5 |
|
Max |
0.05 |
0.10 |
0.10 |
0.010 |
0.008 |
13.25 |
2.5 |
0.01 |
8.5 |
||
Actual |
0.02 |
0.02 |
0.02 |
0.001 |
1.3 |
0.003 |
12.9 |
2.19 |
0.003 |
8.1 |
Mechanical Properties
per ASTM A370 per ASTM E10 |
|
(YS) 0.2%Yield Strength (MPA) |
(TS) Tensile Strength (MPA) |
YS / TS Ratio(%)
|
Elongation
(%) |
Reduction of Area (%) |
Hardness (HBW) |
|
|
Surface of parts |
|||||||
Min |
|
|
|
|
|
|
|
|
Max |
|
|
|
|
|
|
329 |
|
Actual |
|
|
|
|
|
|
|
Macrostructure test as per ASTM A604 |
Class 1 |
Class 2 |
Class 3 |
Class 4 |
||||
Freckles |
White Spots |
Radial Segregation |
Ring pattern |
|||||
A |
Better than A |
A |
Better than A |
A |
Better than A |
B |
Better than B |
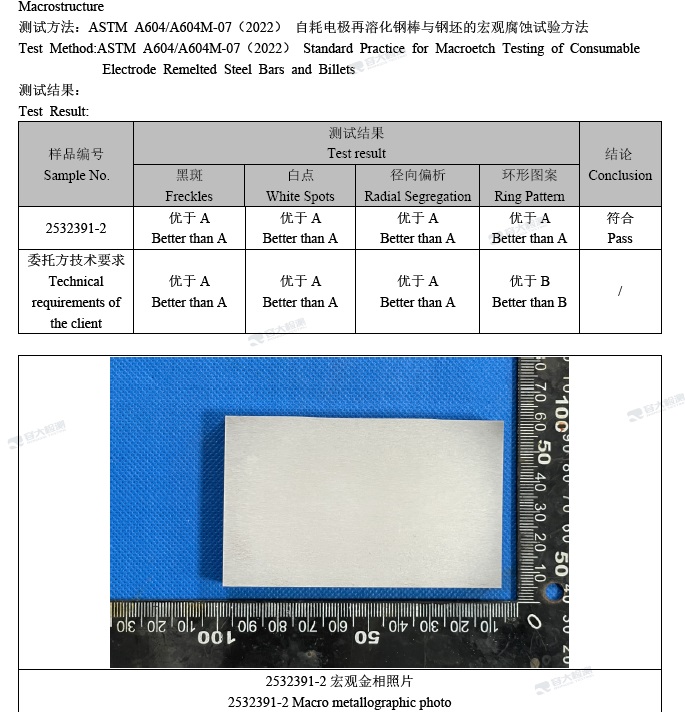
Grain size test report of Ph13-8Mo round abvrs
Ferrite test report of ph 13-8mo round bars